High-Speed Wire Rod And Bar Composite Line
Basis: Take the 700,000t/y bar and wire rod line project built by Hangji for China East Iron and Steel Group Corporation as an example
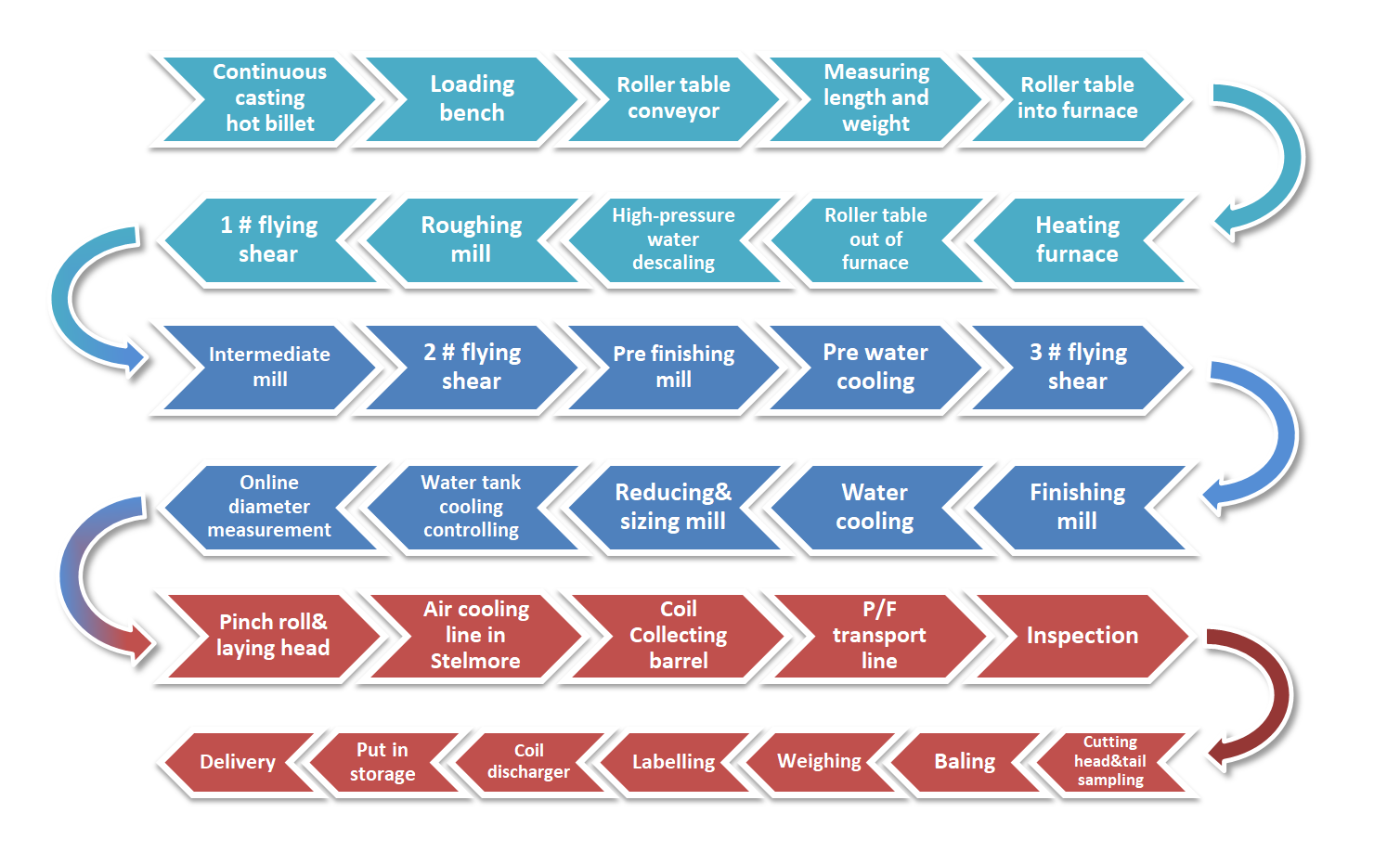
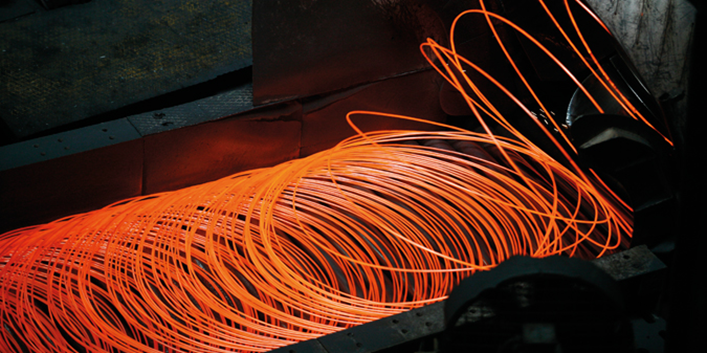
Continuous Casting Rolling
High Output, High Efficiency, Low Energy Consumption, Low Cost
1. Overall Process Design Principles
High output, high efficiency, new technology, new equipment, compact layout, reduced investment
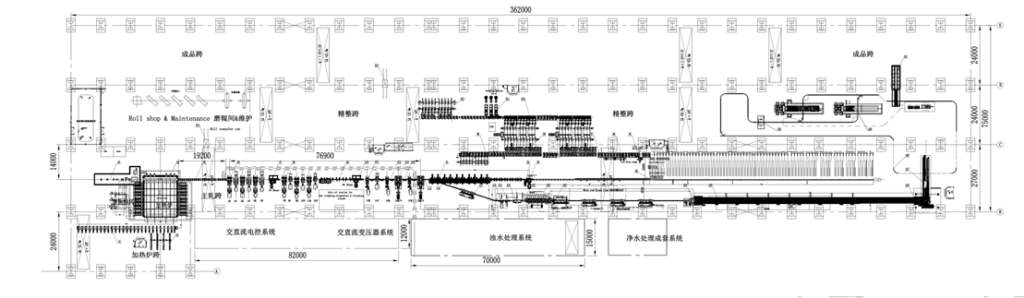
2. Layout Of Main Equipment For High Speed Wire Rod And Bar Line
The rough and medium rolling areas are arranged on the floor (rolling elevation 800mm).
The pre-finishing mill, the finishing mill and its auxiliary and subsequent equipment (up to the laying head) are arranged on the 2200mm platform. The elevation of the rail surface is 11m (the rolling elevation is 3000mm).
3. Production process of bar and wire rod rolling
The 150*150*12000mm billet is hot sent through 4 H-V φ550 mills for single rolling and then enters 2 stands of φ550, 6 stands of φ450 and 6 stands of φ320 mills for horizontal rolling.
After 18 passes of bar rolling, the rolled pieces enter 2 stands of 285 H-V pre-finishing mills and then enter the 3 stands of φ230 plus 5 stands of φ170 Morgan type no twist finishing mills of 45° top cross. The max design speed of the finishing mill is 125m/s and the guaranteed speed is 100m/s.
A single wire rod is rolled for 28 passes of continuous rolling. The pre-finishing mill and the finishing mill adopt no twist and no tension rolling to improve the dimensional accuracy of the product.
There are also laying machine, loose coil air-cooled conveyor, coil collecting station, P&F line, baler, unloading station equipment included for wire rod rolling.
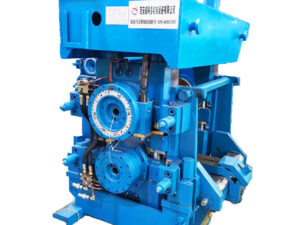
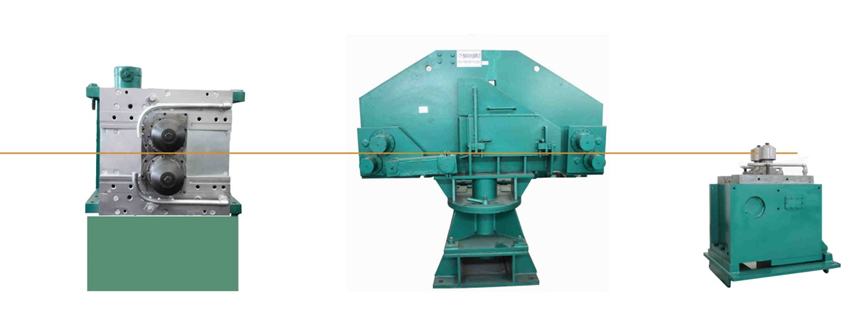
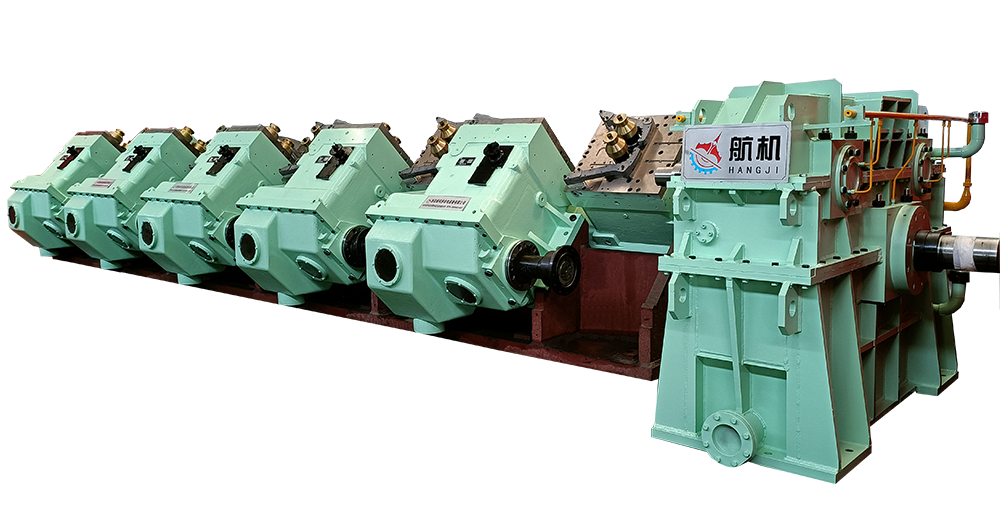
4. Product output and specifications
The design scale is hot rolling wire rod with an annual output of 700,000 tons.
Wire rodφ5.5~φ14.0mm (smooth wire rod)
Wire rodφ8.0~φ14.0mm (threaded wire rod)
Bar φ10~φ32.0mm
Coil parameters:
Inner diameter: Φ850mm
Outer diameter: Φ1250mm
Roll weight: 2000kg
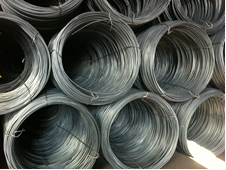
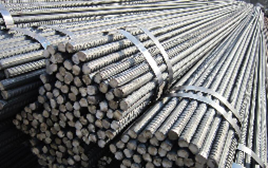
5. Rolling steel grades
High-quality carbon steel, cold heading steel, spring steel, ordinary carbon steel, high and low alloy steel, welding rod steel, etc.
6. Workshop work system and annual working hours
Adopt a continuous working system of four shifts and three operations, and there is no rest during holidays. The annual effective working time is about 7000 h.