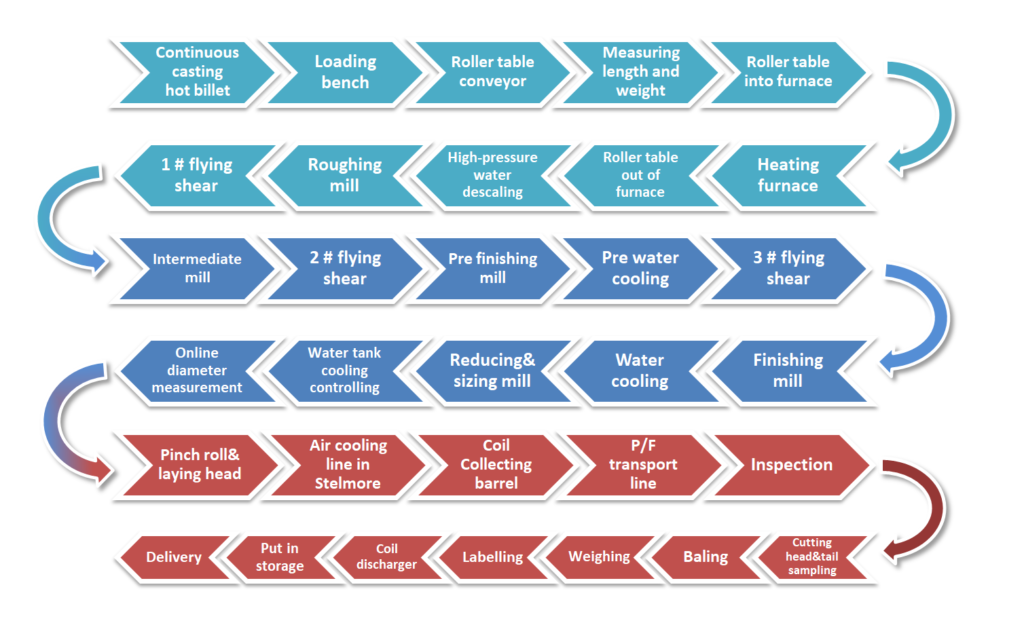
Before entering the furnace
During normal production, the continuous casting billets are hoisted by an electromagnetic disk crane to a charging platform on a platform of+5.0m. The eccentric wheel rotation mechanism of the charging platform conveys the billets forward in a step-by-step manner. The pneumatic blocking device at the output end of the platform descends, causing the billets to slide one by one onto the charging roller table. The feeding roller conveys the blank forward, and it is weighed by a blank scale installed in the roller table. The weight of each blank is automatically displayed and recorded. The automatic length measuring device measures the length of the blank during the transportation of the charging roller table, so that the blank can be accurately aligned after entering the heating furnace.
Billet heating
After the billet enters the heating furnace and stops at a fixed position, the steel pusher located at the end of the furnace will push the billet from the roller table in the furnace in parallel to the fixed beam, and the walking beam will transport the billet forward for heating. The walking beam furnace heats the billet to 1000 ° C~1150 ° C according to the heating system of different steel grades, and the design capacity of the heating furnace is 150t/h (the design capacity of the second high-speed wire heating furnace is 110t/h).
Descaling
The heated steel billet is transported out of the furnace by the roller table inside the furnace, and then the high-pressure water descaling device installed at the furnace outlet descaling the red billet with high-pressure water at a running speed of 0.8~1.5m/s. The steel billet is fed into the first rolling mill of the roughing mill by the front pinch roller on the outlet channel.