Pre finishing mill
The pre finishing rolling mills are cantilever rolling mills. The four stands are divided into two horizontal and two vertical rolling mills. There are three vertical loopers and a safety cover. The arrangement mode is H-V-H-V, which is separately driven by DC motor.
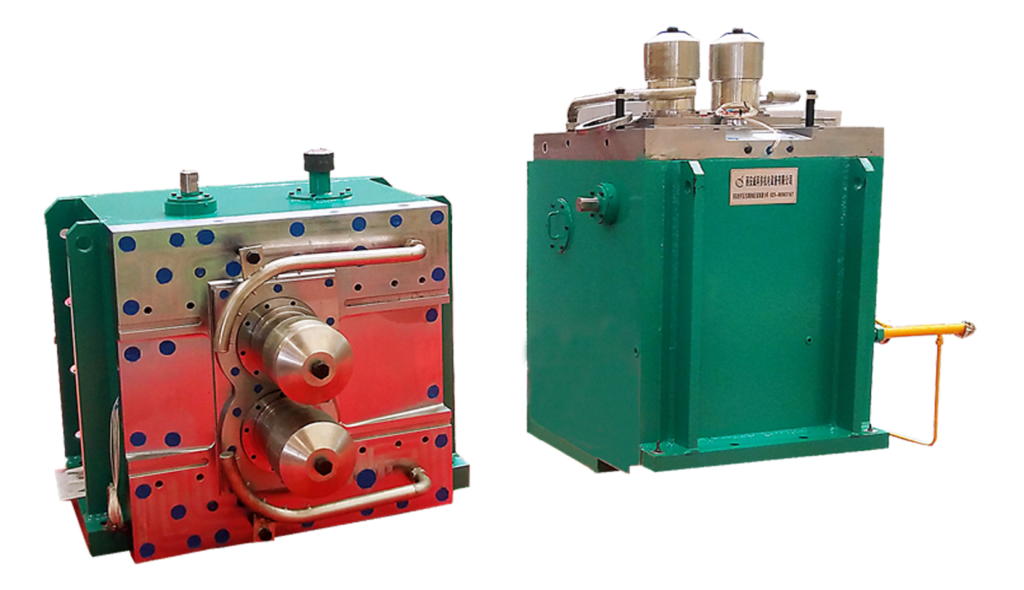
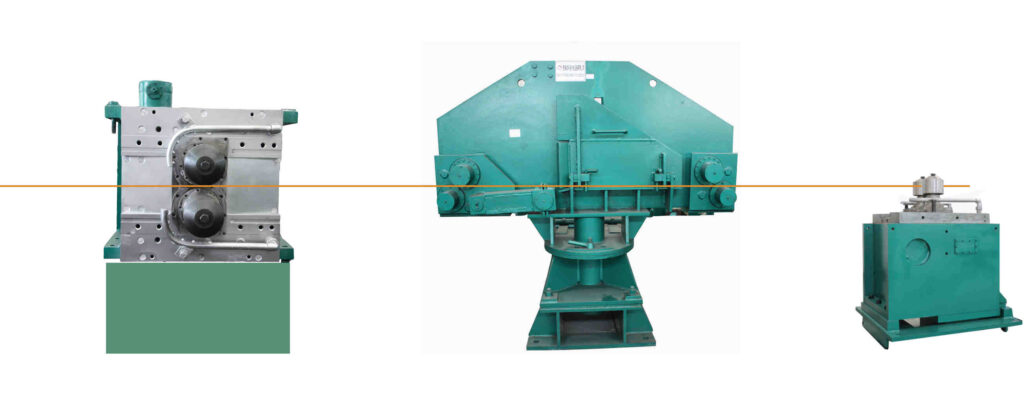
ø285/ø320/ø340/ø385 Pre-finishing mill | |
Brand | Hangji |
Application | High Speed Wire Rod and Bar Rolling |
Finished Product | Φ12-Φ32 Wire rod and bar |
Mill Specification | 2-High ø285/ø320/ø340/ø385 Cantilever mill |
Applicable Annual Capacity | From 300000 to 600000 tons per year |
Applicable Steel grade | Plain carbon steel, alloy steel, tool steel, mold steel, valve steel, titanium alloy, stainless steel |
Max rolling speed | 45m/s |
Equipment application
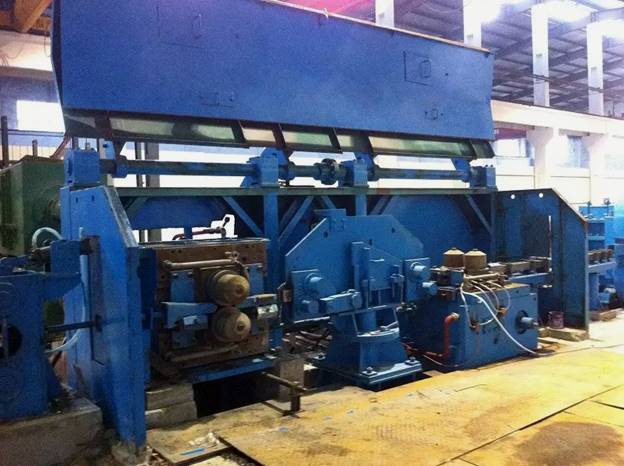
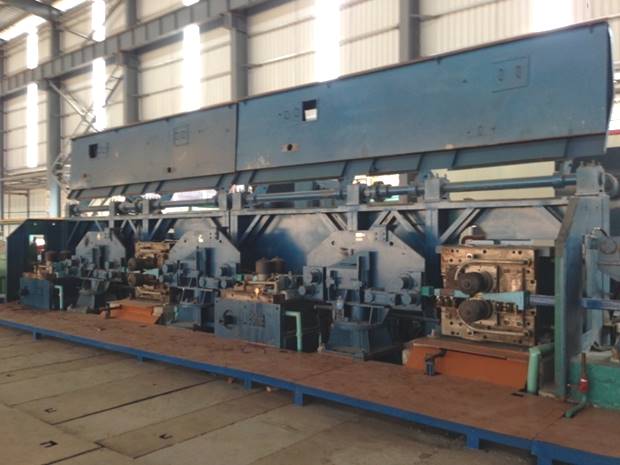
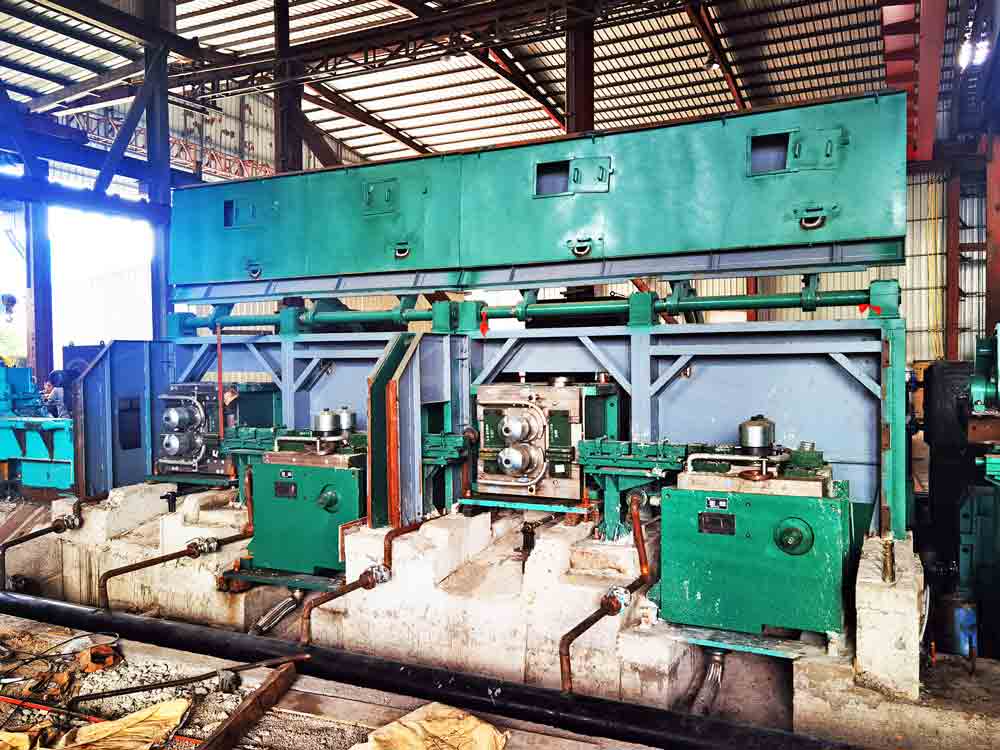
Performance
Low temperature rolling is adopted, and the grain size of the product is increased from Grade 7 to grade 9. The columnar crystal is crushed, and the crystal direction is flaky or granular after crushing, which improves various physical property indexes (yield strength, tensile strength, elongation, etc.)
Through temperature controlled rolling process, the rolled piece is cooled to 780c ˚ After left and right rolling, and then slow cooling, some fine sorbite and troostite crystal orientation components are obtained, which avoids the generation of martensite and coarse pearlite crystal orientation produced by strong water penetration and natural cooling.
When rolling the rebar HRB 400e, according to the requirements of the new national standard, the metal elements V, Ni and Ti shall be added in the molten steel to increase the solid capacity strengthening of the metal bond, so as to improve the physical performance index of the steel. After adopting the low-temperature process of high-strength rolling mill, the content of silicon and manganese alloy in molten steel can be reduced without increasing V, Ni and Ti trace metal elements, and the performance indexes of hrb400e can be guaranteed. Compared with the traditional rolling process, the alloy consumption is reduced by about 30%.
It avoids the defects caused by the rolling method of the strong water penetration process, such as corrosion on the surface of the reinforcement and martensite closed-loop.
The roll is made of tungsten carbide, which improves the surface quality of the finished product after rolling and reduces the consumption of the roll.
Related
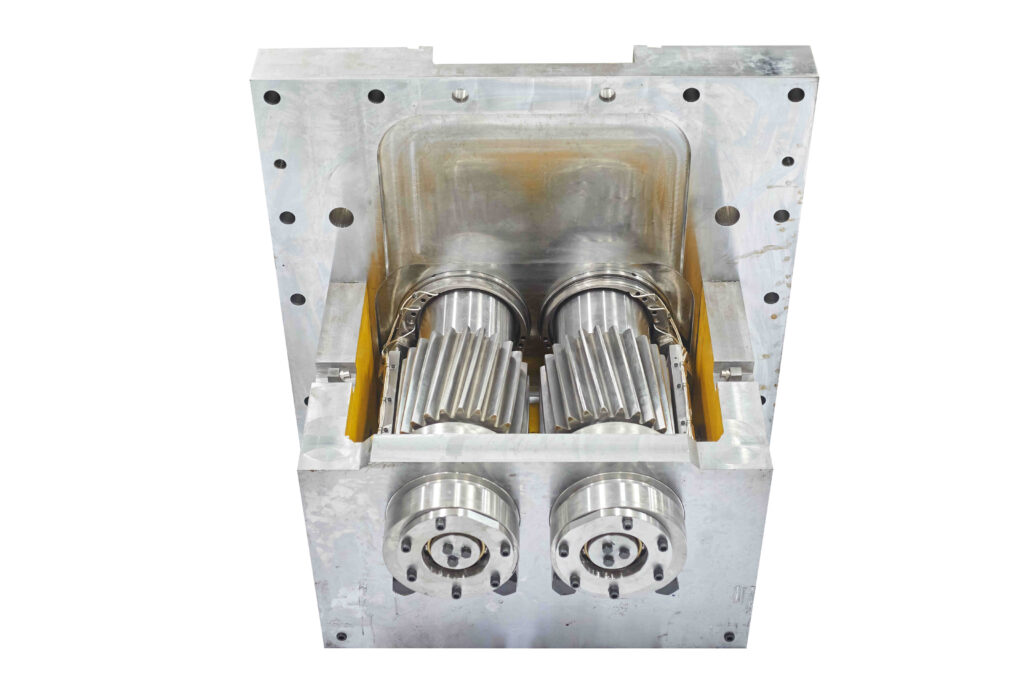
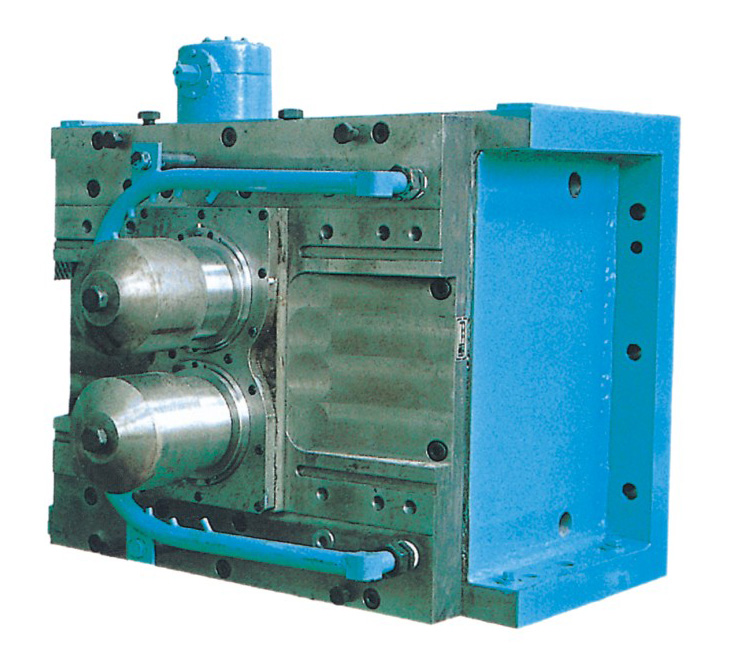
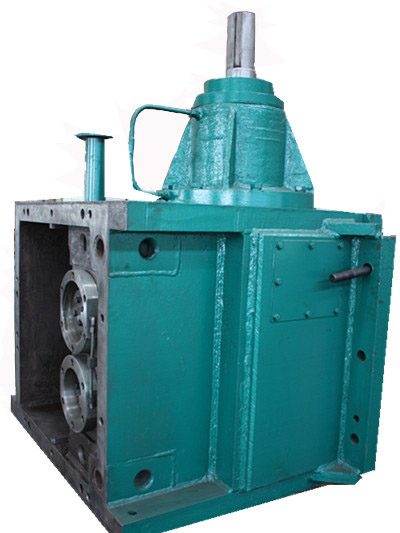