Reducing and Sizing Mill
The Reducing and Sizing Mill (RSM) is positioned between the finishing block mill and the high-speed laying head.
Designed with a split structure and independent twin-module block transmissions, it ensures flexibility and ease of production and maintenance.
This advanced configuration significantly enhances the internal structure and surface quality of the final product.
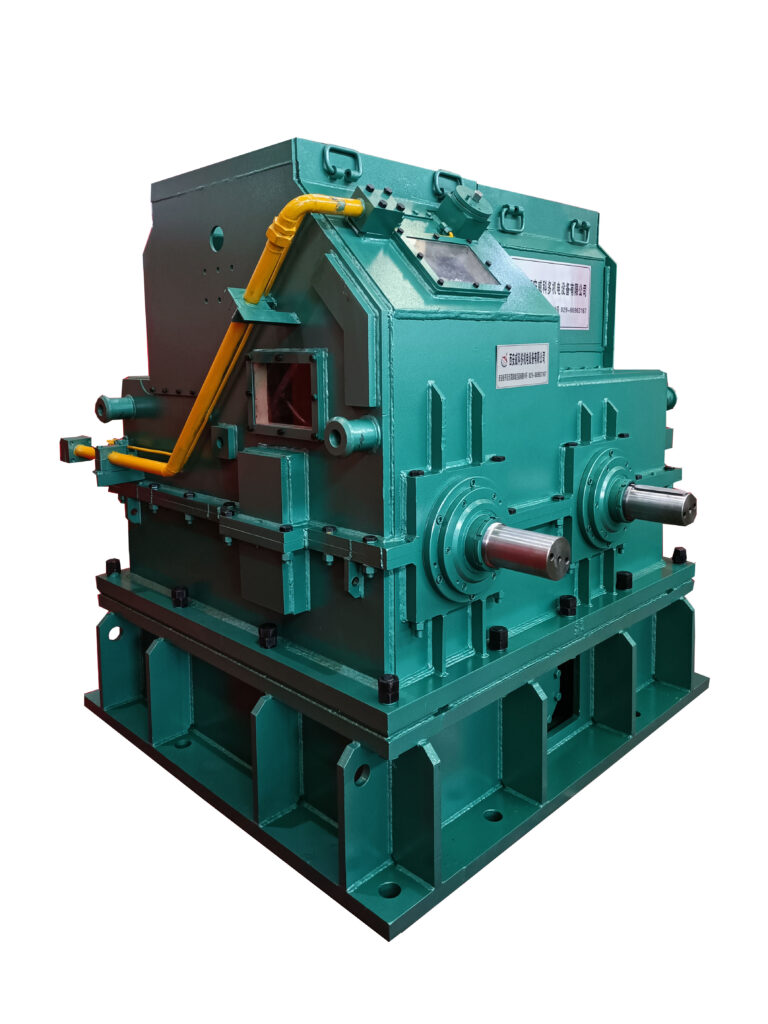
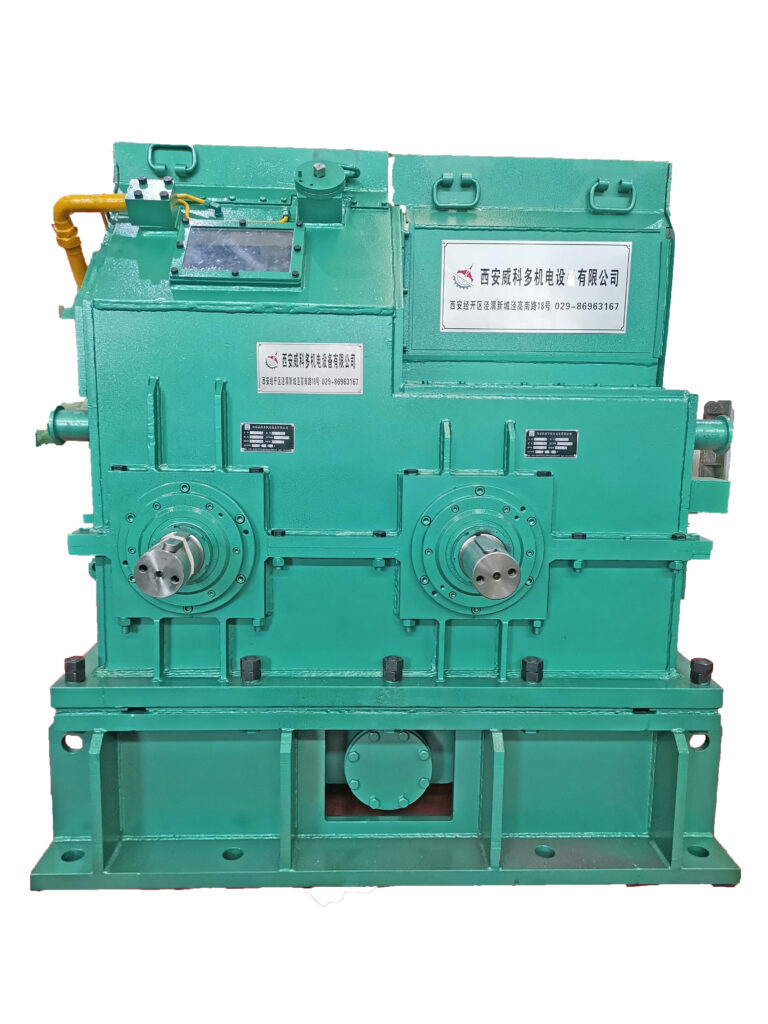
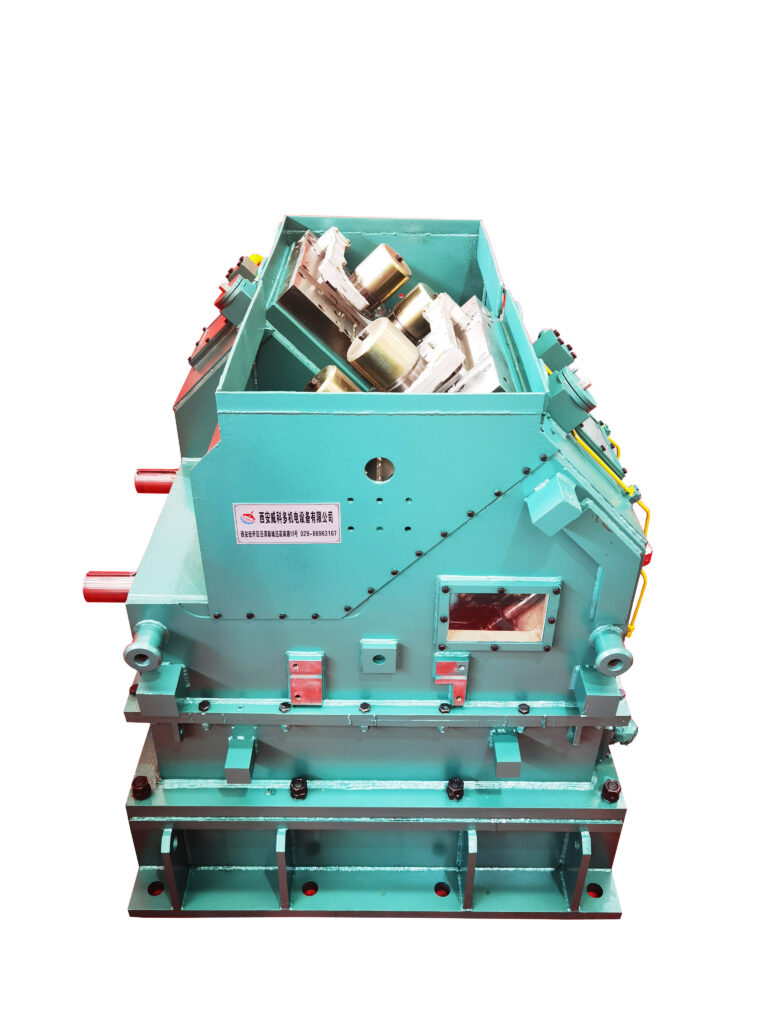
Reducing and Sizing Mill Product Series | ||
---|---|---|
Equipment | Type or Structure | Steel Grade |
150 Sizing Mill | Rolling Bearing Bevel Gearbox + Oil Film Bearing Roll Box Housing | High Speed Carbon Steel Wire Rod Mill |
230 Reducing Mill | All Oil Film Bearings | High Speed Carbon Steel Wire Rod Mill |
230 Reducing Mill | Rolling Bearing Bevel Gearbox + Oil Film Bearing Roll Box Housing | Alloy and Non-ferrous Wire Rod Mill |
230 Twin Module Block | Oil Film Bearings | Low Speed Carbon Steel Small Bar Mill |
250 Twin Module Block | Oil Film Bearings | Low Speed Carbon Steel Small Bar Mill |
265 Twin Module Block | Oil Film Bearings | Low Speed Medium Bar Mill |
330 Twin Module Block | Rolling Bearing Bevel Gearbox + Oil Film Bearing Roll Box Housing | Low Speed Big Bar Mill |
Application
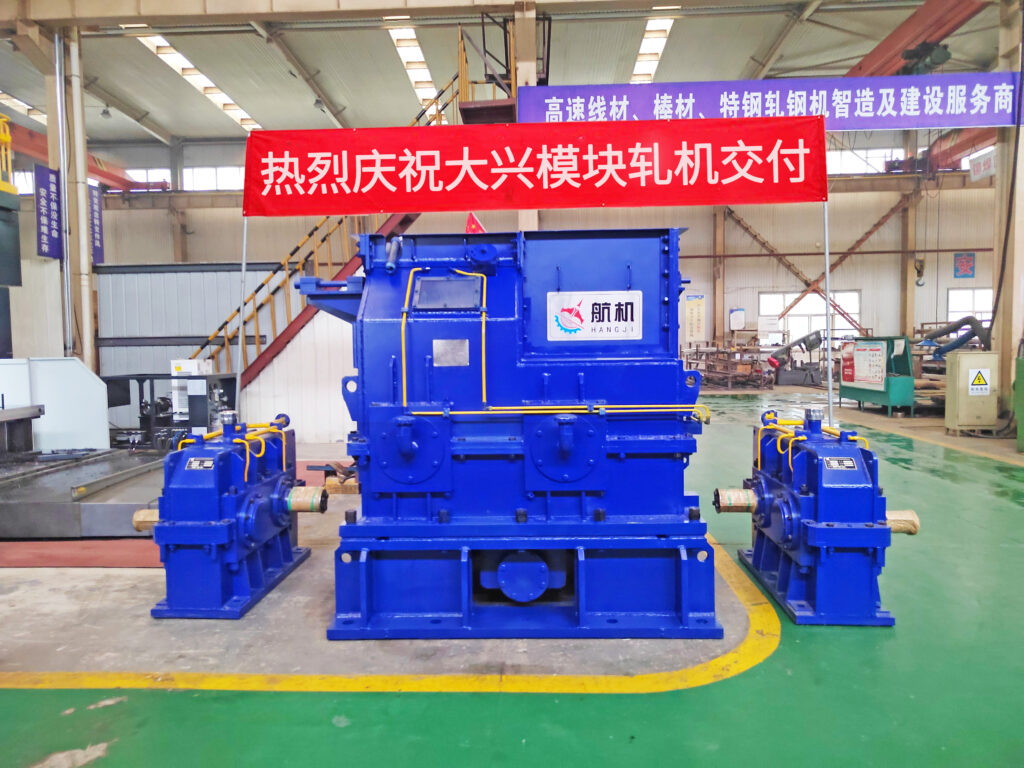
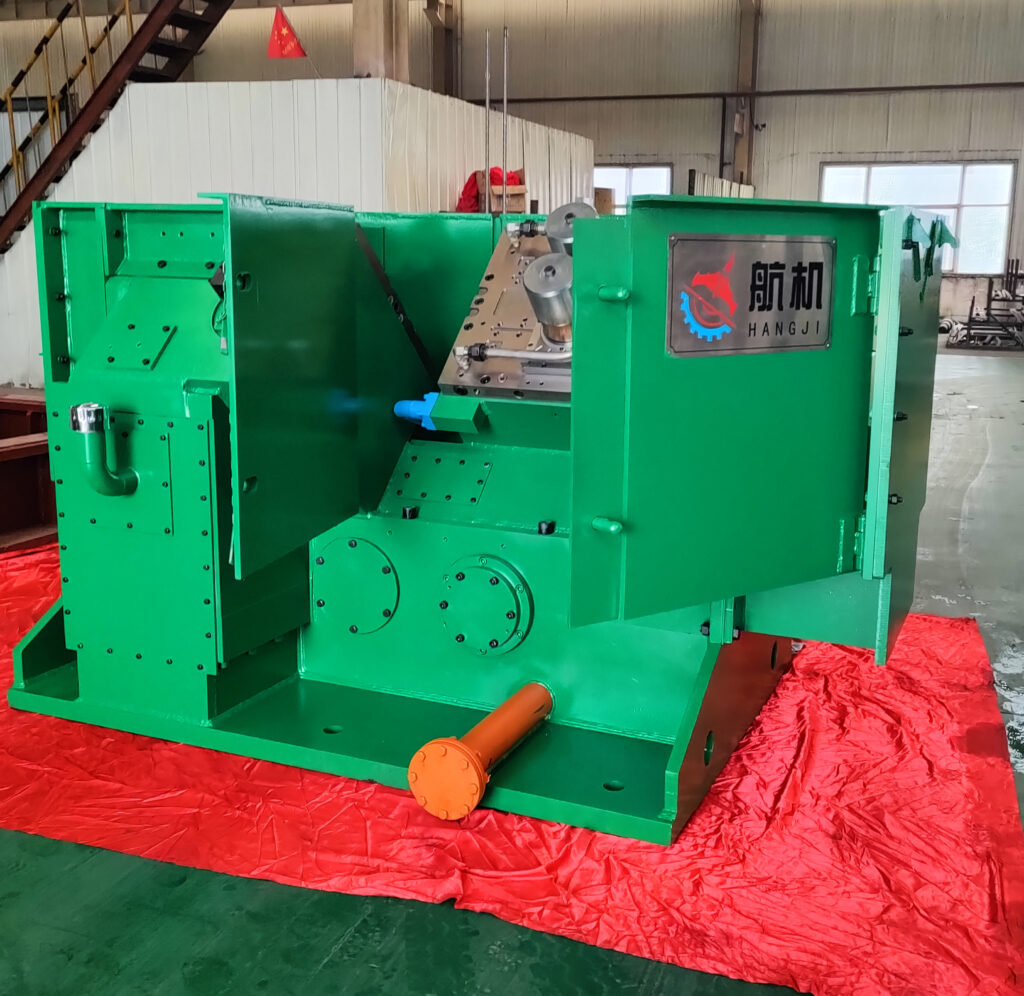
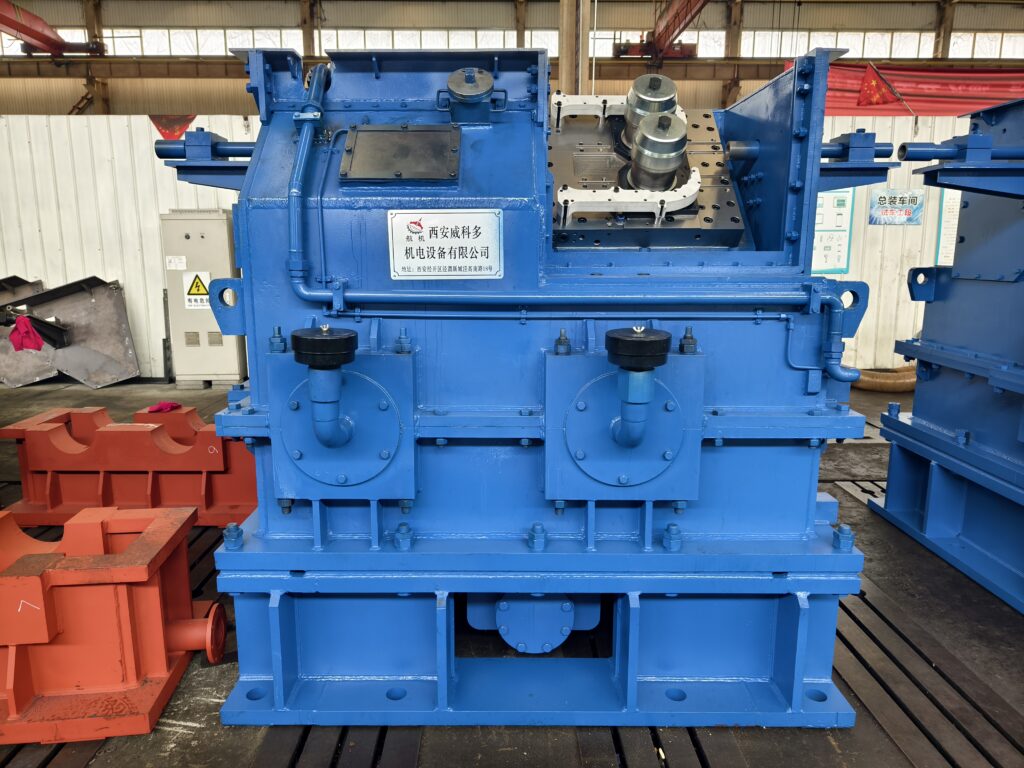
Differences Between
RSM and Conventional Block Mill
• For RSM, The rolling force (KN) will be higher than finishing blocks.
• More flexible than finishing blocks
• Lower prices for spare partsLower power for each RSM`s motor(Low voltage motors can be used)&Lower Electrical Investment
• Lower transmission energy consumption and no-load power
• The bypassing RSM can be stopped to reduce energy consumption and save energy
• When an RSM fails or undergoes maintenance, it can be bypassed or directly replaced with a new block
• Lower prices for spare parts
Outstanding Structure of RSM
• The new high-speed RSM employs dual lubrication systems for the bevel gearbox and roll box, ensuring more thorough equipment lubrication while increasing the number of return oil holes. This effectively eliminates machine burning caused by inadequate lubrication and prevents equipment oil leakage due to enhanced oil pressure and poor return oil flow.
• The cooling water pipes of the high-speed RSM are made of aluminum alloy and designed with a “Snap-On” mechanism, facilitating installation and maintenance. This design allows for easy removal of impurities and blockages in the water circuit and enables swift handling of steel pile-ups.
• The panel thickness of the roll box in the high-speed RSM is 110mm (contrasted with 80mm thickness in other enterprises), and it undergoes nickel-phosphorus alloy plating to prevent corrosion and calcification caused by local water quality. This enhances rolling rigidity and hardness while reducing spare parts wear.
• The bevel gearbox of the high-speed wire rod reducing sizing mill employs a “double long shaft” design for greater stability of the bottom support. The input shaft diameter is increased to ∮145mm (compared to 100mm in other enterprises), enhancing rolling force. Additionally, separate lubrication for gears reduces the incidence of accidents and saves production costs.
• The high-speed RSM adopts a single pass type, facilitating continuous rolling with the preceding finishing block mill and enabling low-temperature rolling.
important things you should know
Questions And Answers
Please provide the following details via Email or WhatsApp so that we can offer suitable solutions and layouts for your project:
1. Project Scope:
Is it new project or renovation project?
2. Raw Material:
Type of raw material (billets or scrap) and its size?
3. Finished Product:
Type of final product (wire rod or bar) and its size?
4. Production Scale:
Your planned annual output in tons?
5. Factory Space:
Available factory size (width and length) for the project?
We are a professional wire rod and bar rolling mill equipment manufacturer with 26 years of experience.
Hangji boasts a comprehensive quality assurance system along with an exceptional quality management team. We adhere to the practice of conducting final inspections and trial operations before shipment.
Simultaneously, we have obtained international certifications for quality systems, including ISO, BV, and SGS.
We have officially established our presence on two B2B platforms (Alibaba, Made-in-China) and operate through two official websites (hangjirollingmill.com, xawkd.com).
Hangji’s factory is located at Xi’an Weikeduo Electrical and Mechanical Equipment Co., Ltd., No. 18, Jinggao South Road, Xi’an City, Shaanxi Province, China.
Explore our factory through the following links:
YouTube:
Factory Video
Google Map:
We extend a warm welcome to customers from both domestic and international markets to visit us.
Since 1998, Hangji has been exporting its products and services to over 20 countries and regions, including but not limited to China, Malaysia, Russia, Thailand, South Africa, India, Ethiopia, the Philippines, Vietnam, Indonesia, and more.
Globally, Hangji has successfully completed over 100 wire rod and bar production lines. Notable clients include Ansteel (China), SinoSteel(China), Yazd Factory (Middle East), Chandan (India), among others.