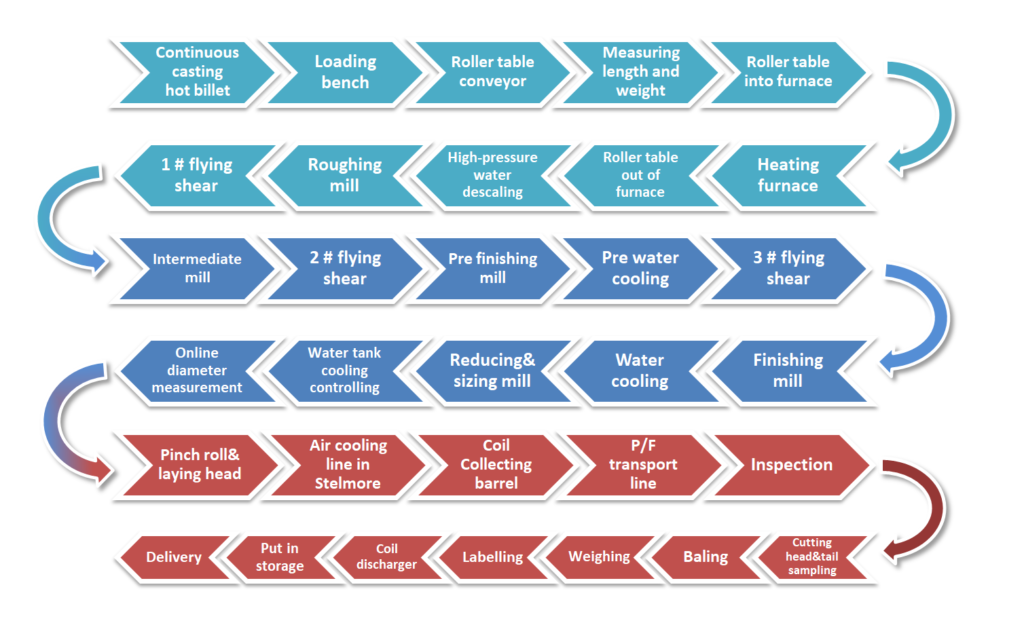
Roughing mill
The steel billet is continuously rolled without torsion in a roughing mill with six alternate horizontal and vertical arrangements. The head is removed by the No. 1 flying shear (the rolled piece can be broken in the event of an accident), and then the rolled piece enters the intermediate mill with six alternate horizontal and vertical arrangements for rolling. The intermediate mill unit is used for micro tension rolling. After the rolled piece exits the intermediate mill unit, it is rolled by the No. 2 flying shear head (the rolled piece can be broken in the event of an accident), and then enters the pre finishing mill unit for rolling.
Pre finishing mill
The pre finishing rolling unit has a total of six rolling mills. The first two stands are both closed end mills, like the roughing and intermediate rolling units. The middle two stands are cantilever roller ring mills, arranged alternately horizontally and vertically, and the last two stands are V-shaped top crossing mills. There are three vertical loops in front of the pre finishing mill, between the pre finishing closed mill, and between the two cantilever roller mills. There is one side loop in front of the cantilever mill and one in front of the V-shaped top crossing mill. After the rolled piece enters the pre finishing rolling unit, the loop is immediately started, so that the rolled piece is in a tension free state between the pre finishing rolling units. The outlet of the side loop is provided with a clamping shear, which can break the rolled piece during an accident state, facilitating accident handling. The looper position of the rolled piece is controlled by a looper scanner and automatically adjusted to maintain the stability of the looper, so that the rolled piece is in a tension free state during the rolling process, thereby ensuring the accuracy of the rolled piece size entering the finishing mill.
Water cooling before finishing rolling
After leaving the pre finishing mill, the rolled piece is cooled by a water tank. Before finishing, two water tanks are provided for pre water cooling to control the temperature of the rolled piece entering the finishing mill. The pre water cooling device adopts closed-loop control, and the water cooled rolled piece enters the finishing mill unit from the flying shear head in front of the finishing mill unit. A pinch roller is installed in front of the flying shear in the finishing mill unit to help transport the rolled piece in the production of large-sized products and accidents. A side loop and a snap shear are arranged in front of the finishing mill. When an accident occurs after the rolled piece enters the finishing mill, the snap shear is immediately activated to prevent subsequent rolled pieces from continuing to enter the finishing mill. At the same time, the flying shear is activated to break the rolled piece, and the switch leads the subsequent rolled piece into the snap shear channel. The snap shear cuts the rolled piece from the pre finishing mill into pieces, which are collected in the waste basket.