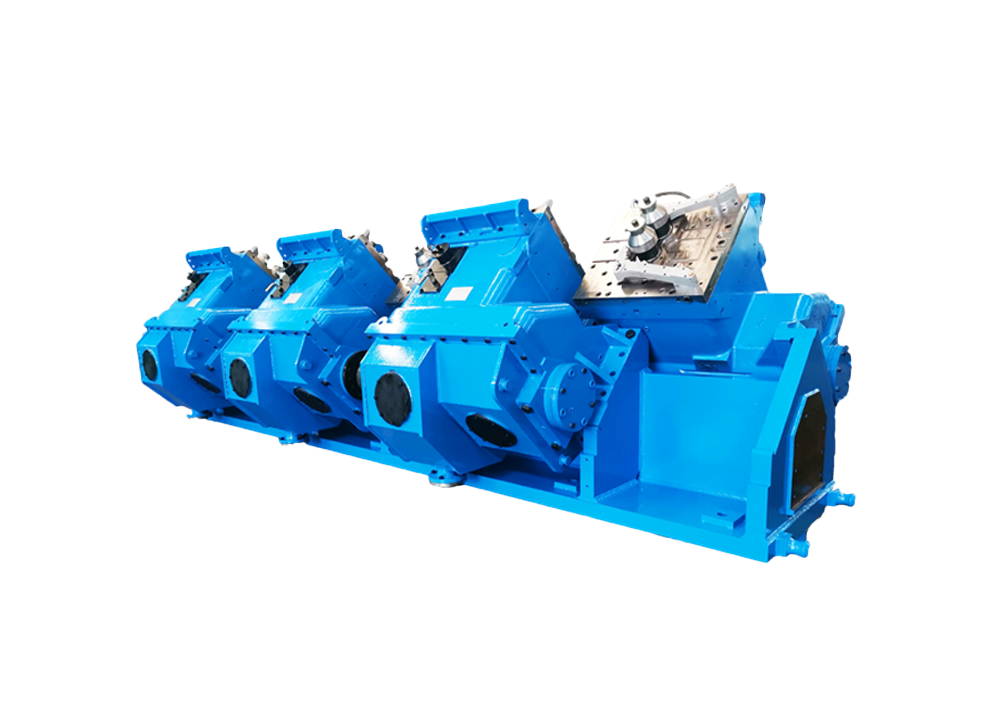
At present, the structure of wire rod mill is very complete. The rolling speed will not be greatly improved or breakthrough improved. However, based on the existing 10 rack and 8+4 structure, it is possible to make small improvements. Here are 8 improvement methods worth discussing.
Increase the blank section appropriately
Increase the blank section appropriately, such as 150 mm × 150mm-160mm × 160mm blank enlarged to 170mm × 170mm-180mm × 180mm. To adapt to the production of different grades of steel and improve the final performance of products. However, it should be noted that the oversized blank section is inappropriate, such as 200mm × 200mm or 220mm × 220mm billets for wire production. Increase the compression ratio of all products to meet the needs of a few products. The increase of production cost will make most products lose competitiveness.
Increase the roll diameter of roughing mill
Increase the roll diameter of roughing mill to obtain fine grains during roughing and improve the metallographic structure and mechanical properties of products.
Replacing traditional closed mill with short stress mill
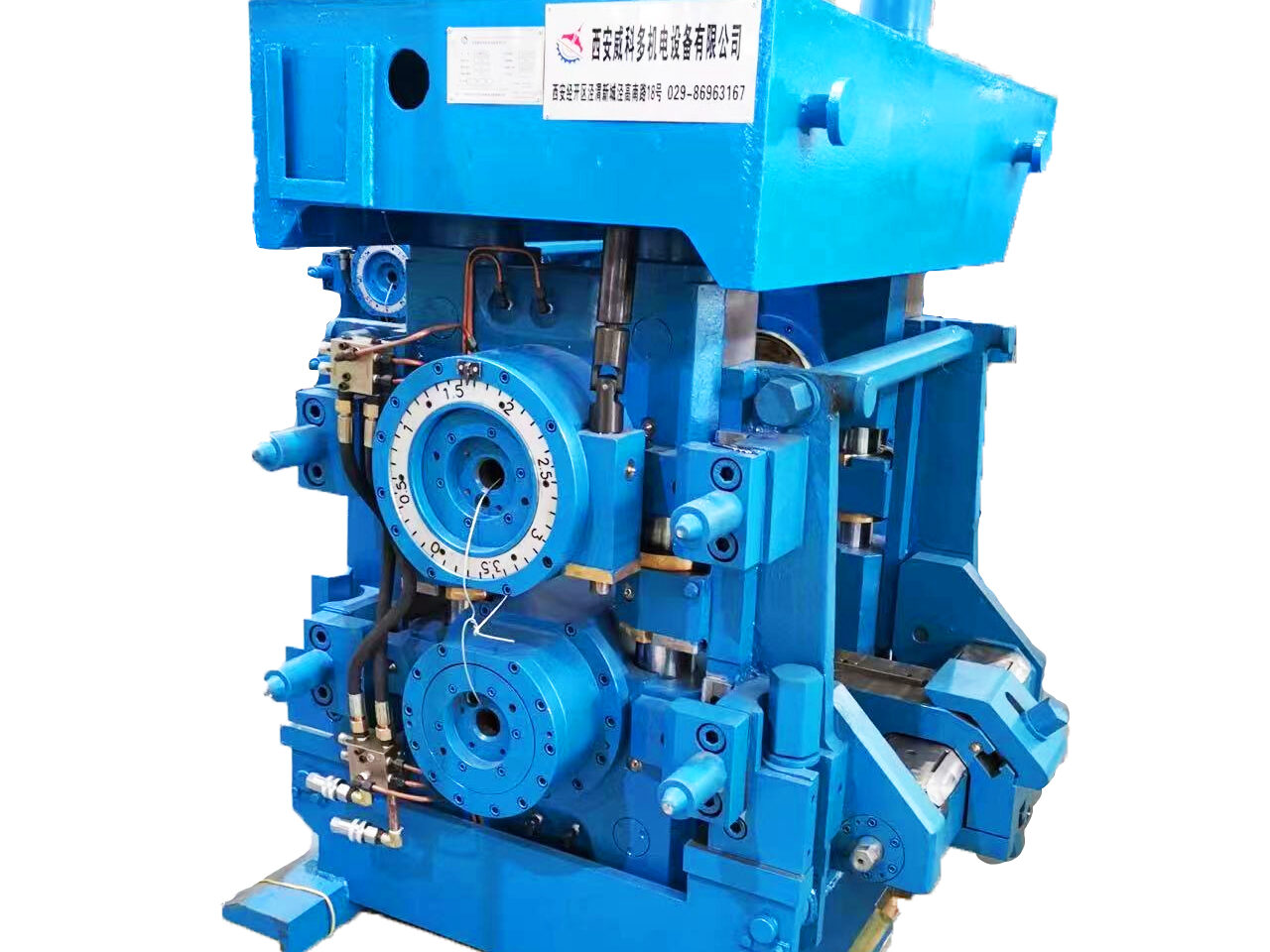
The short stress line mill is used to replace the traditional closed mill to become the roughing and intermediate rolling mills. The short line mill needs a spare stand, and its initial investment is slightly higher than that of the closed mill, but it is simple to operate and convenient to change rolls and stands, which will bring great benefits to production. It is very suitable for high yield wire rod mill.
8+4 type finishing rolling reducing sizing mill
The 8+4 type finishing rolling reducing sizing mill is adopted, which can realize single pass system rolling, reduce pass change and roll change time, and reduce the number of spare parts for rolls and guides; It can improve the size accuracy of wire rod; The low temperature controlled rolling can be realized in full sense, and the mechanical properties of products can be improved; Free rolling can be realized, i.e. delivery according to the product size required by the user. This can fully reflect the advantages of the wire rod mill which mainly produces high-quality steel and alloy steel; But for the wire rod mill mainly producing construction materials, the production cost is increased instead. Therefore, the 8+4 type finishing rolling reducing sizing mill shall be adopted according to local conditions.
Roll box of pre finishing mill
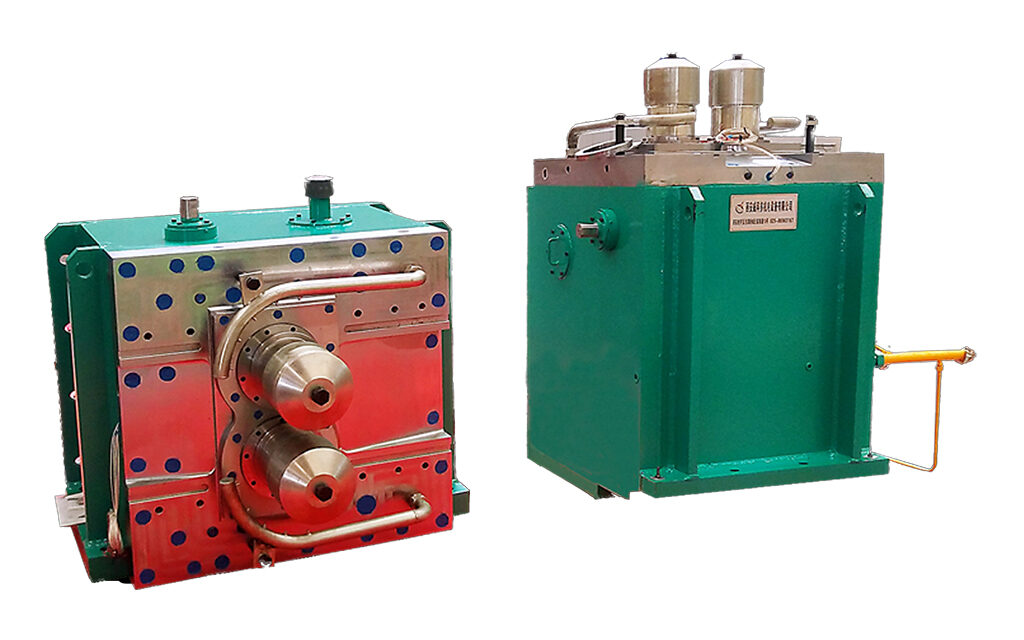
The pre finishing mill adopts the roll box with the same roll diameter and structure as the 8-stand finishing mill and interchangeable with the finishing mill, which can reduce the spare parts and increase the flexibility of the mill.
Flexible loop developed by SMS
The flexible loop developed by SMS is used between the pre finishing mill and the finishing mill, which can shorten the length of the rolling line, increase the temperature uniformity on the section of the rolled piece, more accurately and effectively control the temperature of the rolled piece entering the finishing mill, and realize temperature controlled rolling.
Morgan structural innovation
In addition to the 10 stands and 8+4 stands widely used in wire rod finishing mill, Morgan Company has also introduced two double stand Morgan mills which are driven as a group. This design concept has been put forward for more than 10 years. Unlike in the past, the world’s steel industry has been very calm about it, and there are few responders. For the rolling mill with two stands as a group, it is more convenient to replace the stand, which increases the flexibility of the rolling mill, but the cost of electric control equipment and mechanical equipment will increase significantly. The improvement of its performance is out of proportion to the increase of investment, so no one is willing to take the lead in testing. The Morgan mill with two double stands driven by one set has not been popularized except for a small amount of use in the pre finishing mill. Who would like to try? When can I try? We don’t know. Innovation may not be successful, but most of the wire rod technology innovation led by Morgan has been successful.
Increase fan air volume
The single machine air volume and total air volume of the wire rod air cooling line are increasing. Therefore, increasing the fan air volume can improve the cooling speed of the wire rod and increase the sorbitization rate of high carbon steel to adapt to the production of high carbon steel products such as hard wire and steel cord.
High yield double wire rod mill
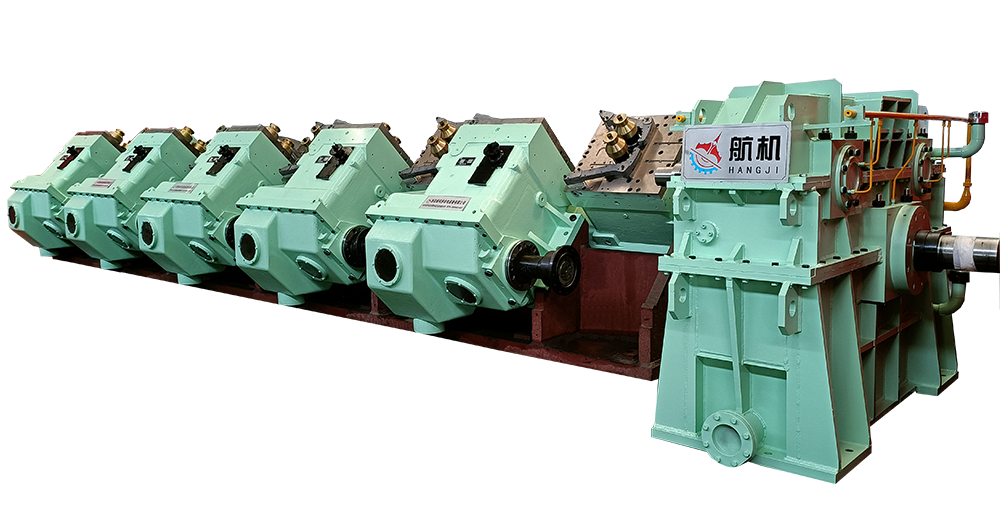
At present, the annual output of the high-yield double wire rod mill, which mainly produces construction steel, has reached 1 million to 1.1 million tons. In China, the demand for continuous increase in output continues. The purpose is to match the high efficiency converter and continuous casting and improve the overall economic benefits of the enterprise. This is a unique phenomenon in China, and other countries may not have such demand.