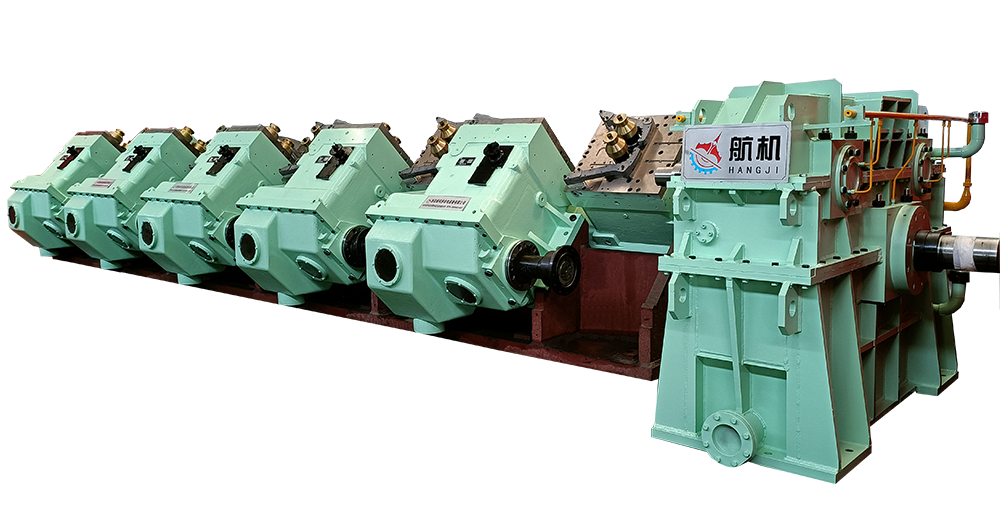
Development of finishing mills
In October 1966, the high-speed non-twist rolling mill developed by Morgan Company with 10-stand collective transmission, cantilevered tungsten carbide small roll ring, side-crossing 45° arrangement, and single-wire non-twist rolling was successfully put into production in Canada, marking the wire rod rolling technology entered a new era.
In the 1960s, the maximum rolling speed of the DC-driven continuous wire rod rolling mill was below 30m/s, and the maximum rolling speed of the tandem type rolling mill was only 15-18m/s. The world’s first Morgan-type high-speed twist-free rolling mill increased the rolling speed to 45m/s.
In the following 40 years, Morgan has led the new trend in the development of wire rod technology in the world, continuously improved the design, and introduced the twist-free rolling mill with newer structure and higher speed to the world. The maximum rolling speed of the rolling mill skyrocketed, reaching 112m/s in the mid-1990s.
Since then, Morgan and Danieli have each developed a 4-stand wire rod reducing and sizing machine, increasing the maximum rolling speed to 120m/s and the design speed to 140m/s. The output of the single-line rolling mill has increased from the initial 150,000 tons/year to 600,000-700,000 tons/year.
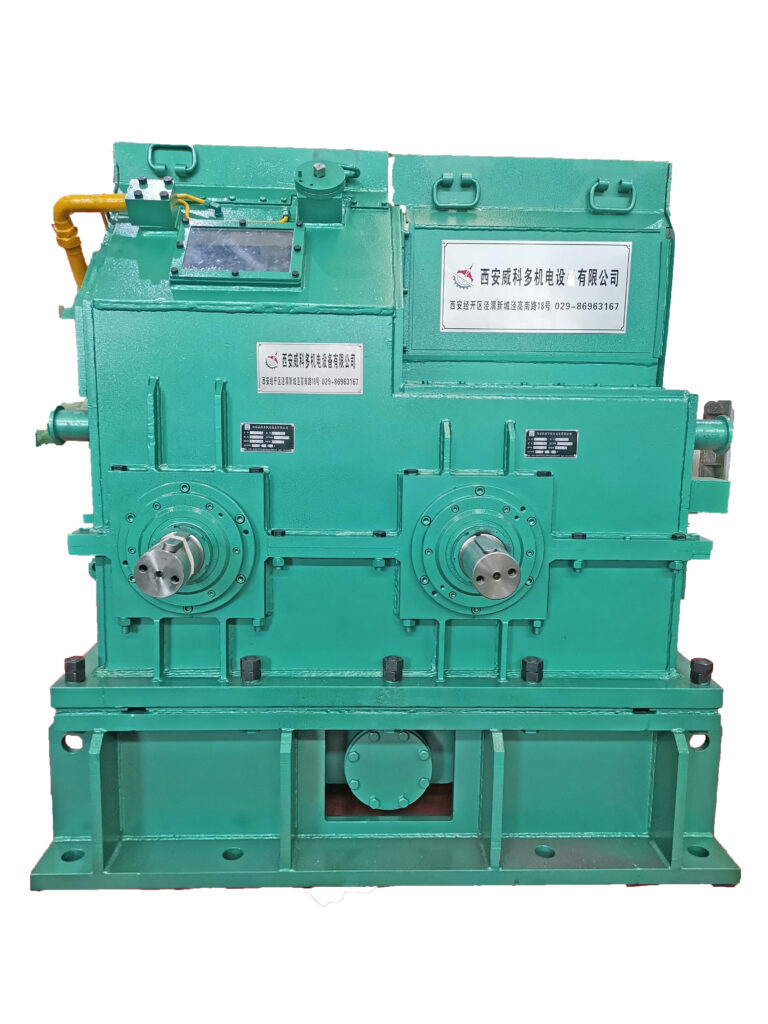
The development of reducing sizing machine
The emergence of the 8+4 reducing and sizing machine marks the change of the development idea of the wire rod rolling mill. From the early stage to improve the rolling speed by improving the structure to achieve the purpose of improving productivity, it has changed to increasing the commonality of the rolling mill pass and reducing the change of holes. Type and roll change time, increase the effective operation time of the rolling mill, and also achieve the purpose of improving the productivity of the rolling mill.
During the nearly 20 years since the mid-1990s, the maximum design speed of the wire rod mill has been stable at 140m/s, the maximum rolling speed is 120m/s, and the guaranteed speed at the minimum roll diameter is 112m/s.
At present, wire rod rolling mills are basically divided into two categories. The first category is wire rod rolling mills with traditional 10-stand finishing mills as the core, and the second category is wire rod finishing mills with finishing rolling mills + reducing sizing machines as the core. The former is mainly used for For the production of ordinary carbon steel and high-quality steel wire rod, the latter is mainly used for the production of high-quality steel and alloy steel wire rod.