Overview
Slit rolling refers to the rolling of a rolling piece longitudinally cut into two or more pieces by using a special roll pass and guide device on a section steel mill, and then rolling out two or more finished rolled pieces.
History
As early as the 18th century, slit rolling has been used for the recycling of old rails, but the continuous production of slit rolling was created in the 1970s by the Canadian United Steel Company Co-steelGroup, and subsequently, the United Kingdom, the United States, and the United States. , Germany, Japan and other countries have also applied this technology. There are many countries in the world that are studying the continuous production of continuous casting billet slitting. In the research, development and practical application of multi-wire slitting rolling, Japan, the United States, Canada, and Germany are at the leading level in the world today, and they have mastered it. The new technology of multi-wire slitting and rolling is promoted to countries all over the world.
Classification
According to whether there are auxiliary devices in the slitting process, the slitting rolling method can be divided into two categories: the pass slitting rolling method and the tool slitting rolling method.
Pass-cut rolling method
The slitting method is to use the rolling of the rolling piece in the slitting pass, and use the pass to cut the rolling piece. Its characteristic is that the deformation and cutting of the rolling piece are carried out simultaneously, without any additional Slicing equipment.
Tool slitting rolling method
The tool slitting rolling method is to use a roll with a special pass to roll the rolling piece into a shape ready to be cut, and then tear the rolling piece into two or Multiple, and then rolled into finished products separately.
Divide
Two-segmenting is the basis of the dividing technology, and three-slicing is the extension and extension of the two-slicing technology.
Tri-slicing is to cut both sides of the rolled piece at one time and divide it into three independent elliptical rolled pieces.
The process of four-slicing is: the first three-slice, the two sides of the rolled piece are cut; the second two-slice, the two connected pieces in the middle are cut again to become 4 independent ovals rolling stock.
Five-cut is a combination of two three-cuts. The first three-cut is to cut the two rolling pieces on both sides, and the second three-cut is to cut the three connected rolling pieces in the middle.
Advantages and disadvantages
Advantages
There are many advantages of split rolling, and the economic benefits are very significant. Whether it is a new rolling mill or an old rolling mill renovation, the split rolling process is more suitable. The main advantages are as follows.
Can reduce the number of stands or use larger section blanks
Under the condition of the same billet section, the split rolling process can be used to reduce the number of rolling stands. On the other hand, under the same conditions of rolling equipment, larger section billets can be used. The economical and reasonable section size of the billet provided by the continuous casting billet is (100 × 100) mm ~ (150 × 150) mm. However, general section steel rolling mills, especially small rolling mills, have certain difficulties in handling billets with this cross-sectional size. It is necessary to increase the number of rolling passes or increase the number of stands on the basis of the original rolling mill conditions. can solve this problem well. The new plant adopts the cutting process, which can reduce the number of racks, and the length of the plant can be shortened, thereby greatly saving investment.
Significant increase in mill productivity
Compared with the traditional rolling process, the split rolling can shorten the rolling time to speed up the rolling rhythm and increase the machine-hour output. When split rolling is used to produce small and large section products, the mill productivity can be approximately the same, so that the capacity of the furnace and other equipment can be effectively utilized.
High product accuracy
Compared with ordinary double-wire rolling, the precision of slitting rolling can be improved by 5% to 20%. Because, first of all, the split rolling process is adopted, and the two rolling pieces that are rolled longitudinally are bitten at the same time, which avoids the error caused by the bending of the roll, and the temperature difference between the head and tail of the rolling material is small; It is not possible to achieve full tension rolling when the root stock passes through the same rolling mill, while split rolling enables tension-free rolling because only a small portion of the entire rolling process is double-rolled.
Reduce energy consumption and costs
Split rolling can shorten the rolling time, so the heat loss of the rolled piece is small, so the temperature of the billet can be reduced by 30 to 40 °C compared with the traditional rolling process, which reduces the energy consumption of metal deformation, so it can save 15% to 20% of electricity. %. Due to the reduction of rolling passes, roll consumption can also be reduced by 15%. All these reductions in consumption can reduce production costs by 10% to 20%.
The hole structure can be changed (change the asymmetric hole to the symmetrical hole)
In section steel rolling, the adjustment of the asymmetrical pass and the control of the dimensional accuracy of the product have always been difficult problems to solve when producing products with asymmetrical cross-sections. By means of split rolling, two asymmetrical cross-sections can be rolled into one symmetrical cross-section for rolling. , and finally cut and formed, which solves the above problems well.
Suitable for connection with continuous casting machines
Small rolling mills can use the slitting process to eat continuous casting billets with larger sections. Even wide slabs can be cut into billets of different specifications by the slitting method and supplied to the rolling mill, so that the continuous casting machine can only cast slabs with a few cross-sectional sizes, which is beneficial to improve the output of the continuous casting machine and the casting process. The quality of the billet can be improved, and the problem of unqualified billet section size and the mismatch of the output of the continuous casting machine and the rolling mill can be solved to a certain extent, so as to better solve the problem of the connection between the continuous casting machine and the rolling mill.
Shortcoming
Slit rolling also has disadvantages, which are caused by uneven deformation, generally as follows.
After slitting, the rolled piece is bent laterally in the horizontal plane.
The cut sample has a camber bend, and the curvature is large, which is conducive to the realization of cutting, but if the curvature is too large, it will increase the difficulty of turning the steel, transporting and biting in the subsequent passes.
Surface fold
When the slits are not neat, the burrs and burrs of the slits form surface folds after rolling. In addition, when the cutting and rolling positions of the previous and subsequent passes are not repeated, the surface of the billet will also be folded.
Surface defects
Shrinkage cavities, inclusions and segregation of steel ingots and continuous casting billets are mostly located in the center, and are easily exposed to the surface after being cut, forming surface defects.
Bar mill
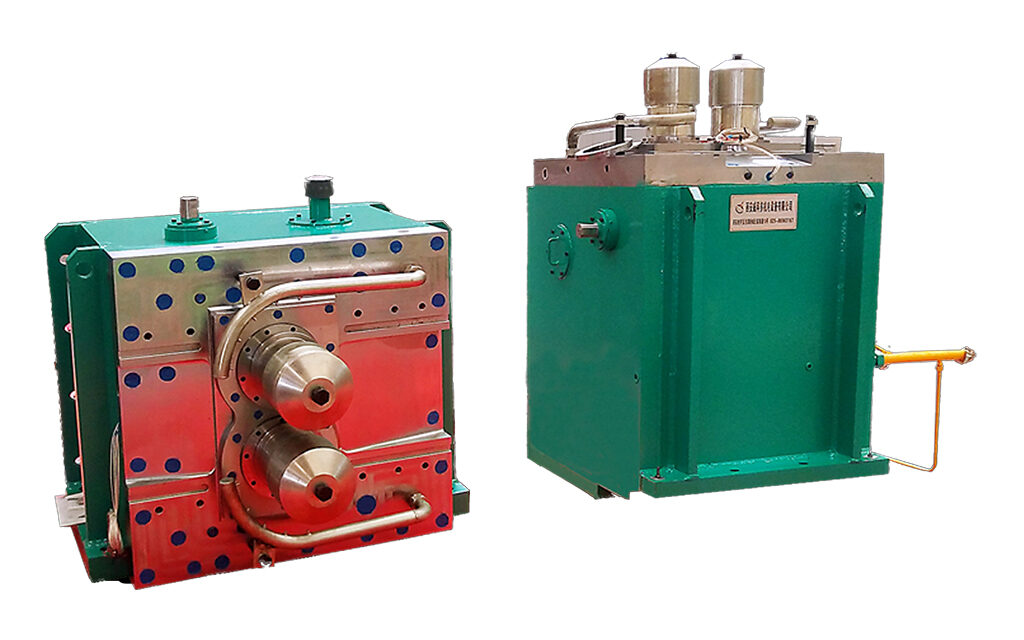
Wire Rod Mill
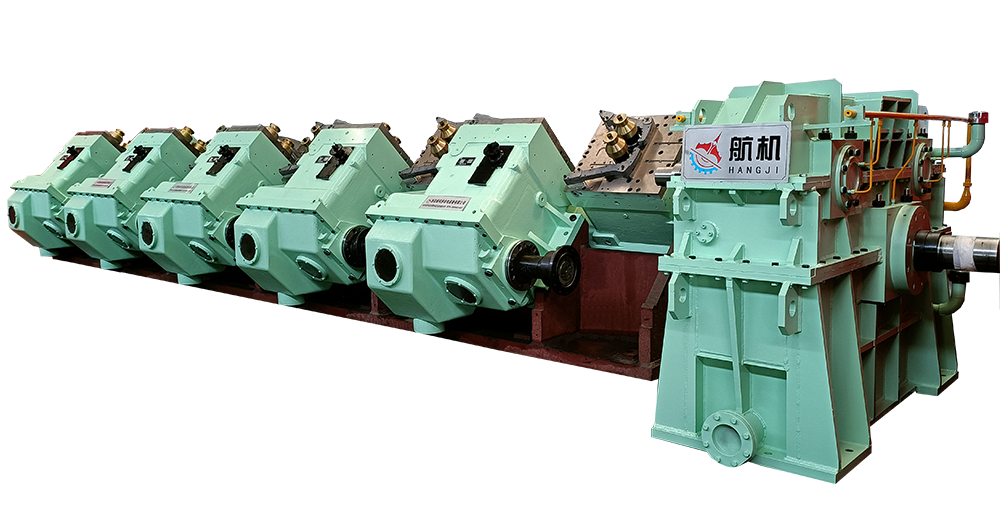